Common Myths and Misconceptions About Aircraft Cables

Aircraft cables play a crucial role in various applications within the aviation and rigging industries. However, there are several myths and misconceptions surrounding these essential components that can lead to misunderstandings and potential safety issues. In this article, we'll debunk some of the most common myths about aircraft cables and provide accurate information to help rigging professionals make informed decisions.
Myth 1: All Aircraft Cables Are the Same
One of the most prevalent misconceptions is that all aircraft cables are interchangeable. In reality, there are significant differences in cable types, materials, and specifications.
Aircraft cables come in various constructions, including:
- 7x7 (49 wires)
- 7x19 (133 wires)
- 1x19 (19 wires)
Each construction offers different characteristics in terms of flexibility, strength, and resistance to fatigue. Additionally, cables can be made from various materials such as stainless steel, galvanized steel, or specialty alloys, each with its own unique properties.
Myth 2: Aircraft Cables Don't Require Regular Inspection
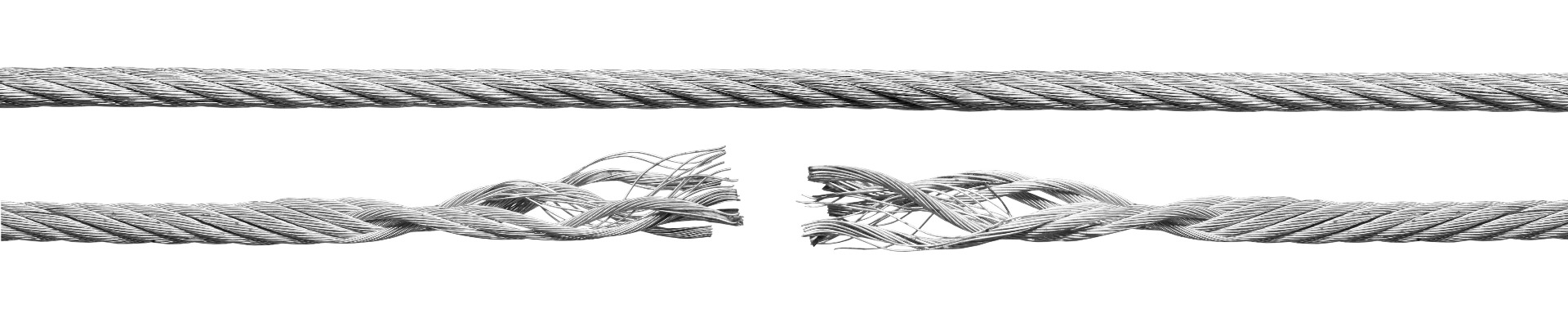
Some believe that once installed, aircraft cables don't need regular inspection. This is a dangerous misconception that can lead to catastrophic failures.
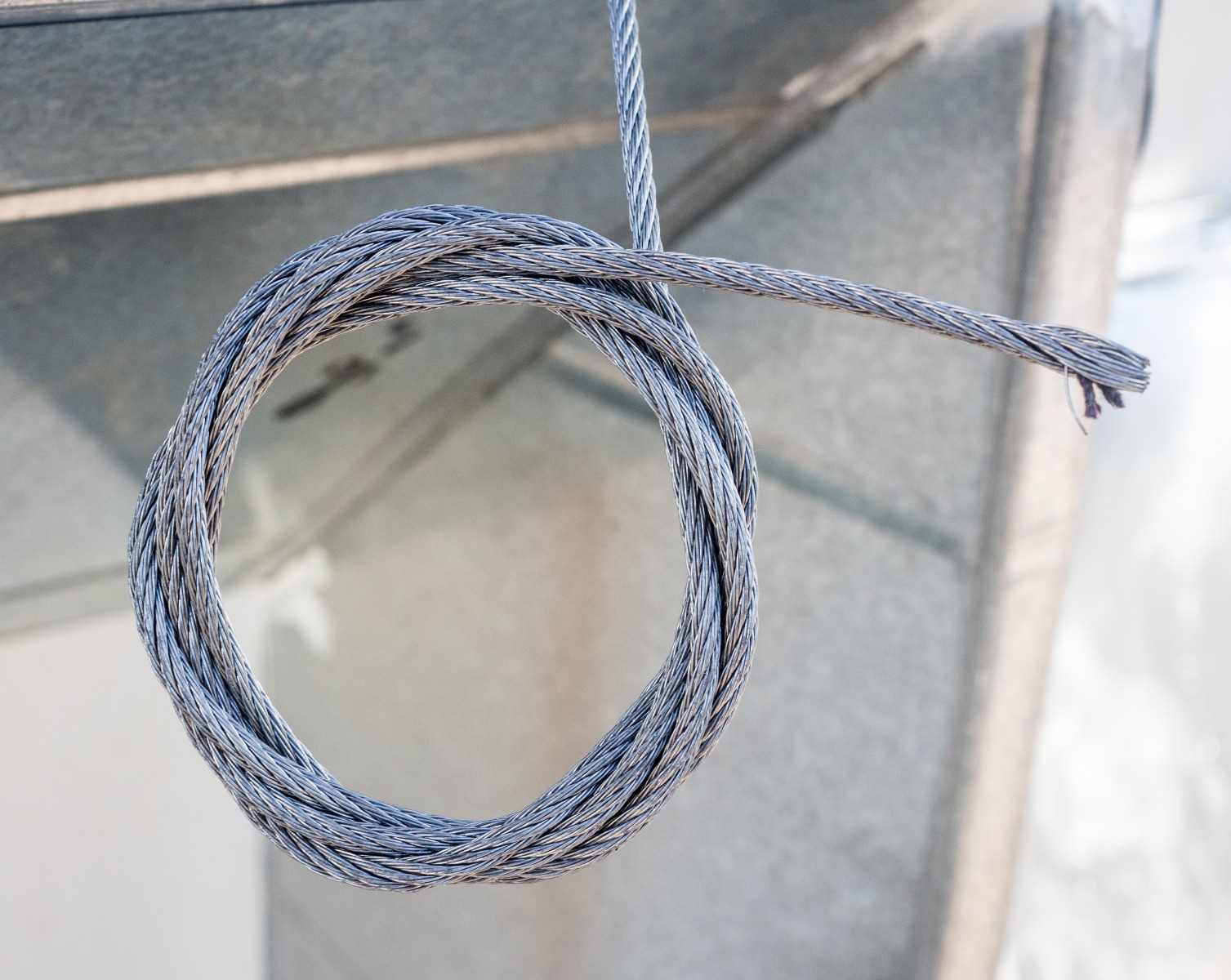
In fact, regular inspections are critical for ensuring the safety and integrity of aircraft cables. The Federal Aviation Administration (FAA) recommends thorough inspections at regular intervals, checking for:
- Broken wires
- Kinks or sharp bends
- Corrosion
- Wear and fraying
- Proper tension
Regular inspections can identify potential issues before they become serious problems, ensuring the longevity and safety of the rigging system.
Myth 3: Higher Breaking Strength Always Means Better Performance
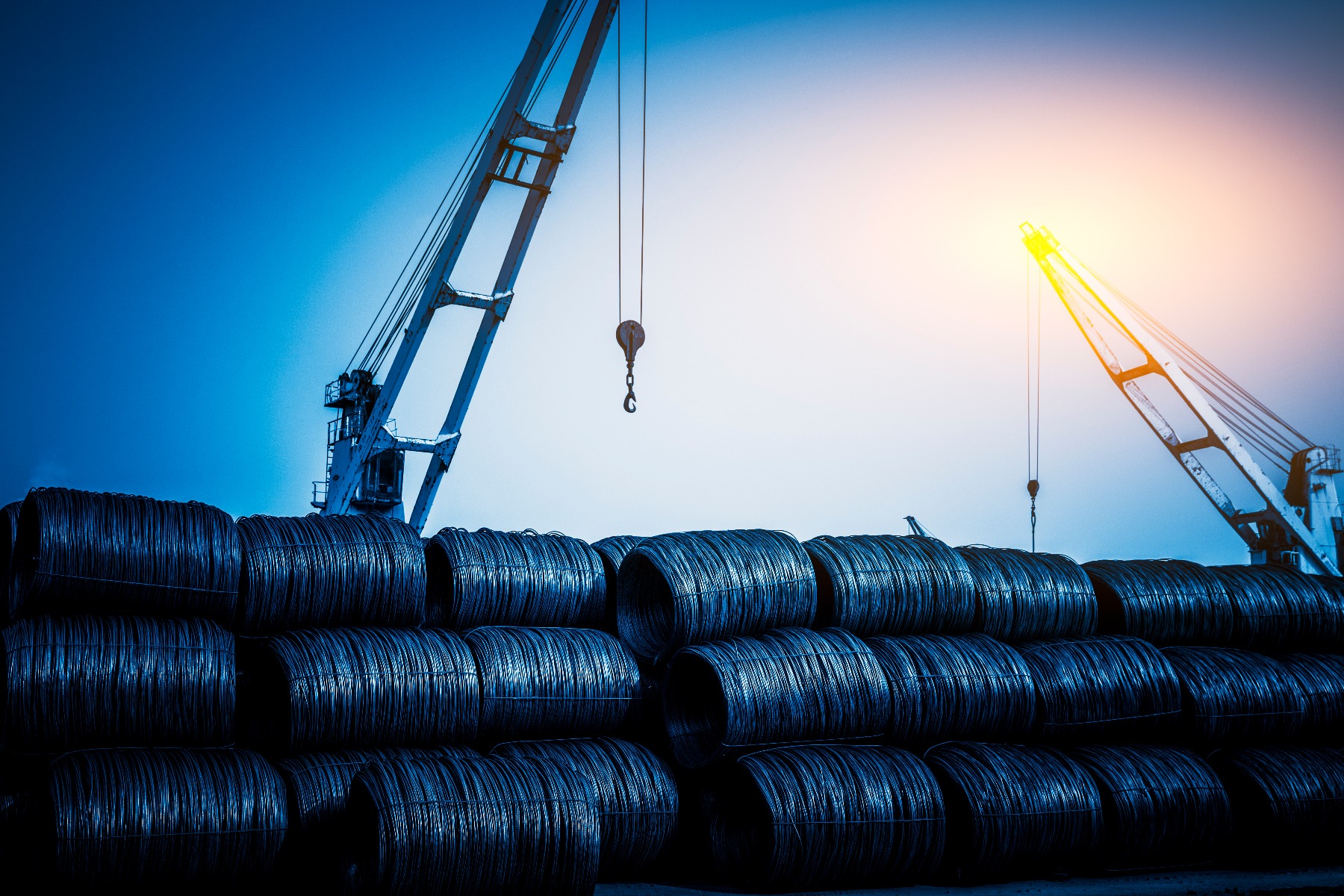
While breaking strength is an important factor, it's not the only consideration when selecting an aircraft cable. Other crucial factors include:
- Fatigue resistance
- Flexibility
- Corrosion resistance
- Weight
- Environmental conditions
Choosing a cable solely based on breaking strength without considering these other factors can lead to suboptimal performance or even failure in certain applications.
Myth 4: Stainless Steel Cables Are Maintenance-Free
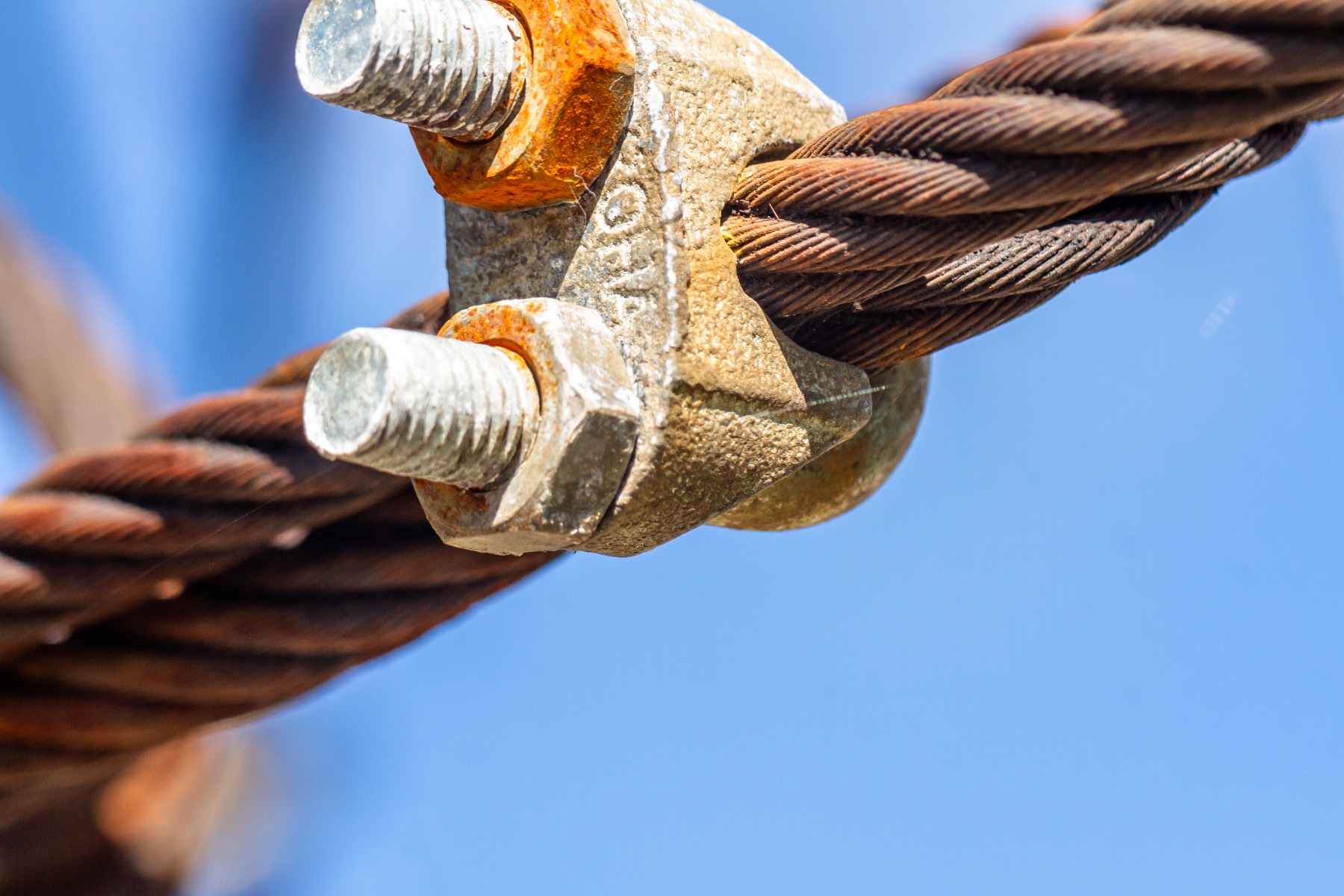
Stainless steel aircraft cables are often touted as maintenance-free, but this is not entirely accurate. While stainless steel offers excellent corrosion resistance, it still requires proper care and maintenance.
Regular cleaning, lubrication, and inspection are necessary to ensure optimal performance and longevity. Neglecting maintenance can lead to issues such as:
- Reduced flexibility
- Increased wear
- Potential for stress corrosion cracking
Proper maintenance practices should be followed regardless of the cable material.
Myth 5: DIY Cable Assemblies Are Just as Good as Professional Ones
Some may believe that creating their own cable assemblies is a cost-effective alternative to professional fabrication. However, this can be a dangerous misconception.
Professional cable assemblies offer several advantages:
- Precise swaging and termination
- Proper tension setting
- Quality control measures
- Compliance with industry standards and regulations
DIY assemblies may lack the precision and quality assurance necessary for critical applications, potentially compromising safety and performance.
Conclusion
Understanding the truth behind these common myths and misconceptions is crucial for anyone working with aircraft cables in the rigging industry. By dispelling these misconceptions, we can ensure safer, more efficient, and more reliable rigging systems.
Remember, when it comes to aircraft cables, always consult with experts, follow manufacturer guidelines, and adhere to industry standards and regulations. Proper selection, installation, and maintenance of aircraft cables are essential for the safety and success of any rigging operation.