Wire Rope Construction and Its Uses in the Rigging Industry

Wire rope is a crucial component in the rigging industry, known for its strength, durability, and versatility. Understanding the various wire rope constructions is essential for selecting the right rope for specific applications. This blog post will focus on four common wire rope constructions: 1x7, 7x7, 7x19, and 1x19, exploring their characteristics and uses in the rigging industry.
1x7 Wire Rope Construction
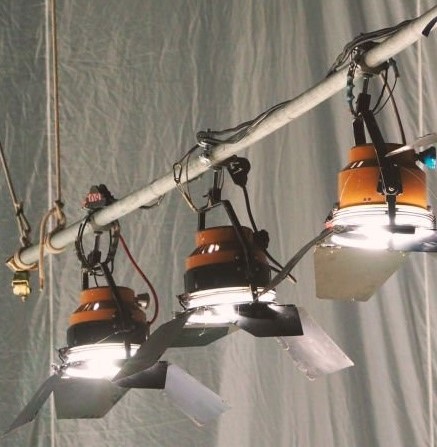
The 1x7 wire rope consists of a single strand with seven individual wires. This construction offers:
- High strength-to-diameter ratio
- Excellent resistance to abrasion
- Low stretch characteristics
Uses in Rigging:
- Guy wires for towers and antennas
- Standing rigging in marine applications
- Overhead power transmission lines
- Cable barriers in road safety systems
7x7 Wire Rope Construction
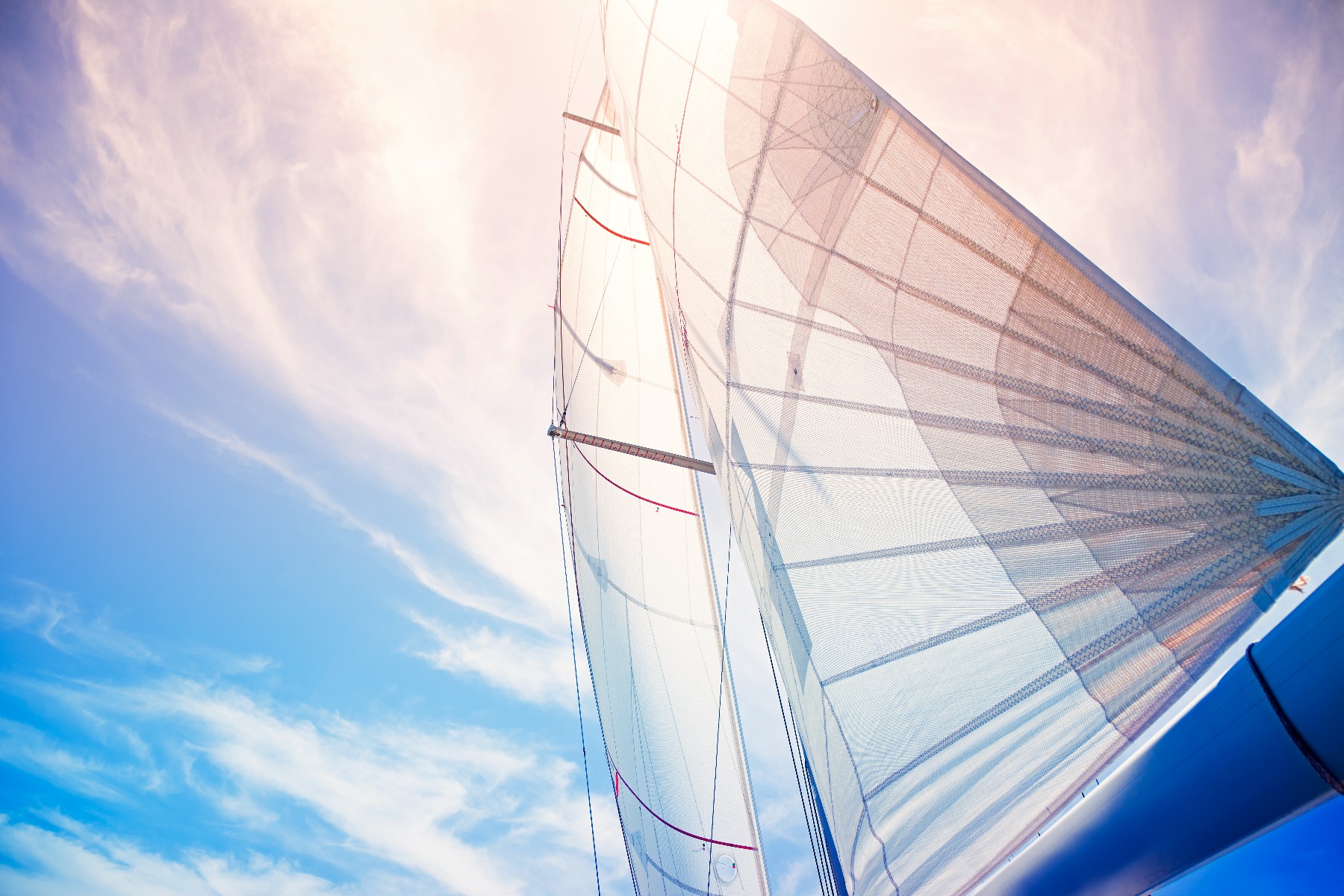
The 7x7 wire rope features seven strands, each containing seven wires. This construction provides:
- Increased flexibility compared to 1x7
- Good strength-to-weight ratio
- Moderate abrasion resistance
Uses in Rigging:
- Aircraft control cables
- Small diameter lifting applications
- Sailboat rigging
- Light-duty hoisting operations
7x19 Wire Rope Construction
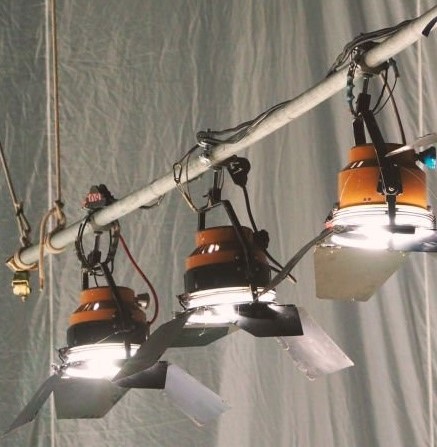
The 7x19 wire rope consists of seven strands, each containing 19 wires. This popular construction offers:
- Excellent flexibility
- Good fatigue resistance
- Smooth operation over pulleys and sheaves
Uses in Rigging:
- Crane hoist lines
- Winch cables for off-road vehicles
- Elevator systems
- Stage rigging in theatre's
1x19 Wire Rope Construction
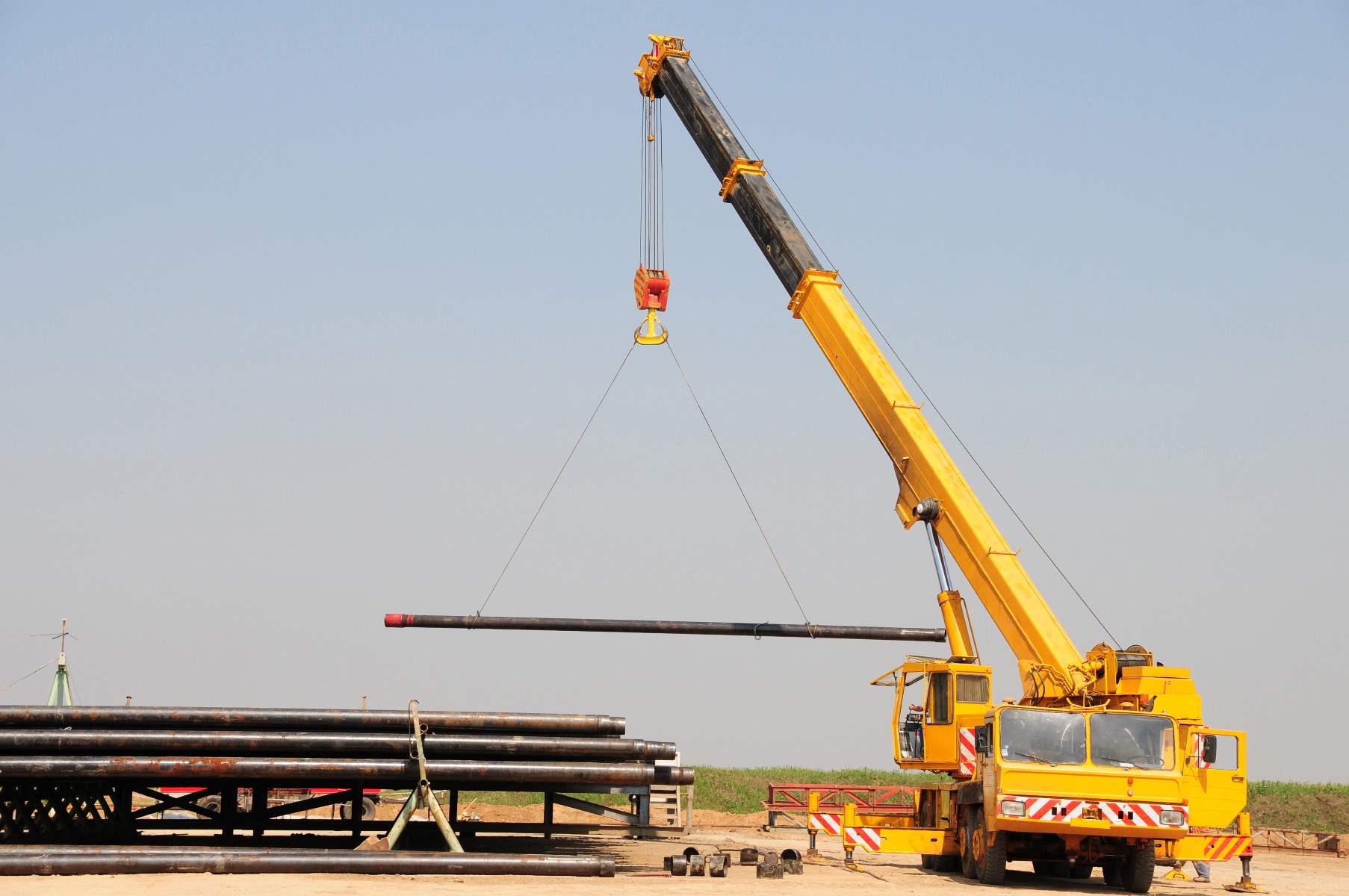
The 1x19 wire rope is composed of a single strand with 19 individual wires. This construction provides:
- Very high strength-to-diameter ratio
- Excellent resistance to abrasion
- Low stretch characteristics
Uses in Rigging:
- Structural cables for bridges
- Prestressing tendons in concrete structures
- Guy wires for large communication towers
- Tension members in architectural applications
Factors Influencing Wire Rope Selection
When choosing between these wire rope constructions for rigging applications, consider the following factors:
- Strength requirements - This refers to the maximum load the wire rope must safely support. It's crucial to select a rope with a breaking strength well above the maximum anticipated load, typically using a safety factor determined by industry standards or regulations.
- Flexibility needs - This factor considers how often the rope will need to bend around sheaves or drums. More flexible ropes (like 7x19) are better suited for applications requiring frequent bending, while less flexible ropes (like 1x7) are preferable for static loads or where minimal stretch is desired.
- Abrasion resistance - This relates to the rope's ability to withstand wear from contact with surfaces or other objects. Ropes with fewer, larger outer wires (like 1x7 or 1x19) generally offer better abrasion resistance than those with many smaller wires.
- Fatigue life - This factor is important in applications where the rope undergoes repeated bending cycles. Ropes with more wires per strand (like 7x19) typically have better fatigue resistance due to the distribution of stresses across more wires.
- Corrosion resistance - The rope's ability to resist degradation from exposure to moisture, chemicals, or other corrosive elements is crucial, especially in marine or industrial environments. The choice of wire material (e.g., galvanized steel, stainless steel) plays a significant role in corrosion resistance.
- Operating environment - This encompasses various environmental factors such as temperature extremes, exposure to chemicals, presence of abrasive materials, and frequency of use. The operating environment can influence all other factors and may necessitate specific coatings or materials for the wire rope.
Understanding these factors is essential for selecting the most appropriate wire rope for a given application. The right choice balances these considerations to ensure optimal performance, safety, and longevity of the rigging system. Remember, when in doubt, it's always best to consult with a wire rope specialist who can provide expert guidance based on your specific needs and operating conditions.
Maintenance and Inspection
Proper maintenance and regular inspection are crucial for ensuring the safety and longevity of wire ropes in rigging applications:
- Conduct visual inspections for broken wires, kinks, or corrosion
- Lubricate ropes according to manufacturer recommendations
- Monitor for diameter reduction and rope elongation
- Replace ropes when they reach discard criteria as per industry standards
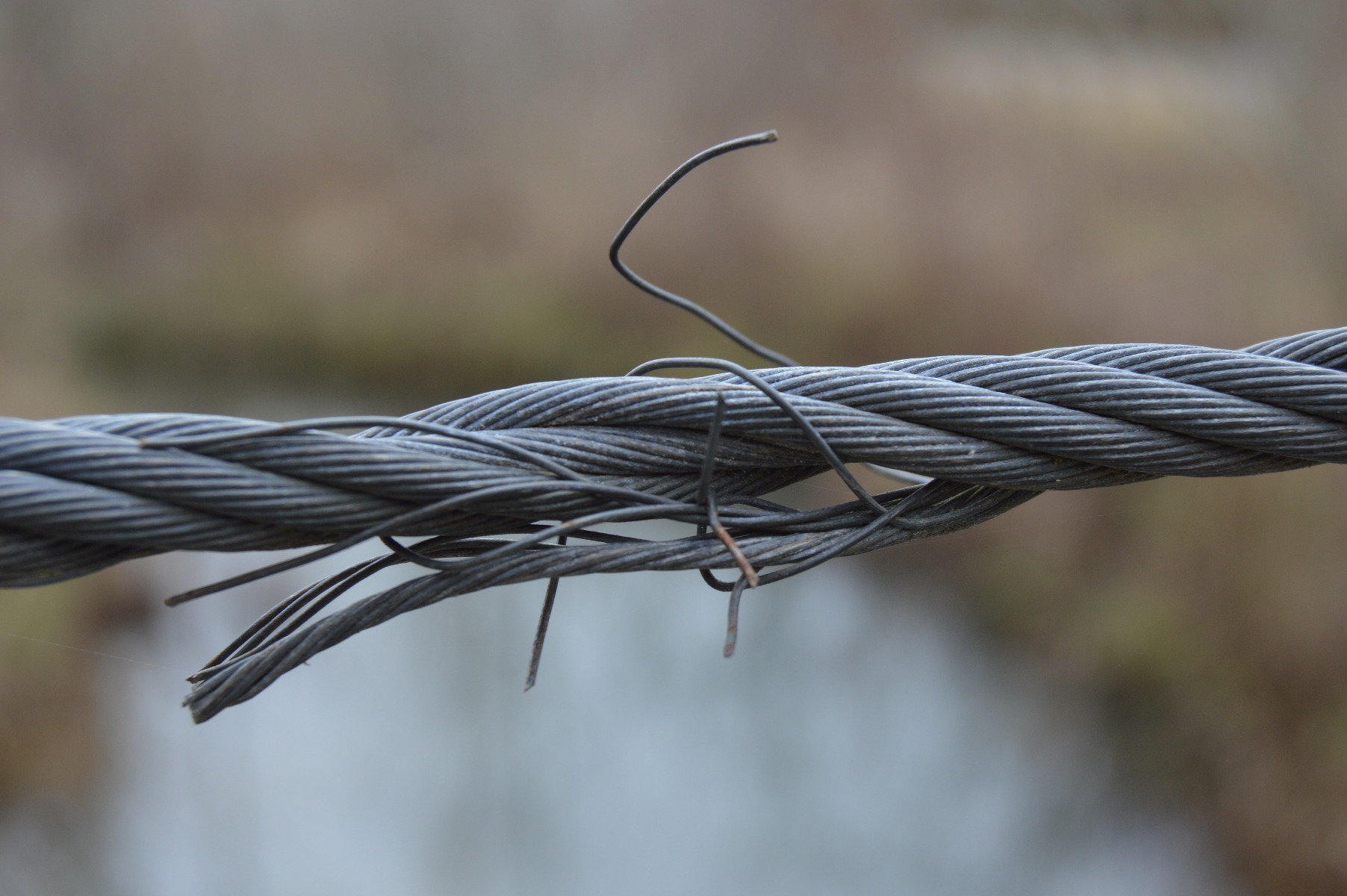
Conclusion
Understanding the characteristics and applications of 1x7, 7x7, 7x19, and 1x19 wire rope constructions is essential for professionals in the rigging industry. Each construction offers unique properties that make it suitable for specific applications. By carefully considering the requirements of each job and selecting the appropriate wire rope construction, riggers can ensure optimal performance, safety, and efficiency in their operations.
Remember, while this guide provides general information, it's always best to consult with wire rope manufacturers or rigging experts for specific application advice. Proper selection, use, and maintenance of wire ropes are critical for safe and effective rigging operations.
At Laureola Industries, we offer a wide variety of wire ropes, known for their exceptional quality and competitive prices. Since 2006, we have been trusted for our reliability, safety, innovation, and outstanding customer support. We are committed to meeting our customers' needs and delivering excellence in every product